How Arecont Vision’s Quality Checks and Technical Support Ensure (Source Security)
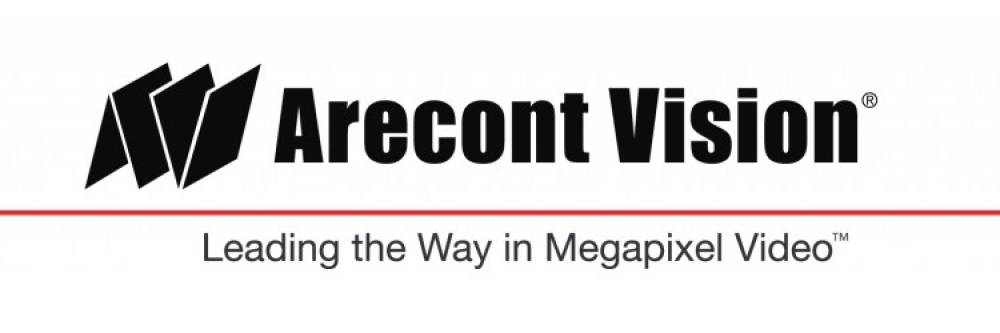
View/download the original article published by SourceSecurity.com here
Can a U.S. manufacturing company compete and thrive in the global security market? Megapixel camera manufacturer Arecont Vision makes a strong case that it can.
Dialogue and integration with VMS companies
Assembling products in the USA helps Arecont Vision ensure quality. If there is a quality issue, the company can stop the production line and fix it. Although some of Arecont Vision’s components, such as camera housings, are manufactured in low-cost regions of the world, including China, everything is assembled in Glendale, California, with additional quality checks. The “Made in USA” tag line is a statement of quality in much of the world, says Scott Schafer, Arecont Vision’s Executive Vice President of Sales, Marketing and Service.
Arecont Vision is expanding its technical support, especially maintaining a regular dialogue with technical support personnel from various video management system (VMS) companies. In effect, the goal is an “on-purpose, proactive teaming in the field” to provide a joint value proposition in the security market. Arecont Vision integrates with more than 100 VMS and NVR companies, including all the big ones such as Milestone, Genetec, Exacq, Lenel, DVTEL, 3VR, and many others. “It depends on what the client wants,” says Schafer.
"We have come a long way in a
|
Faster, stronger technical support for customers
Speed of technical support is another priority, and Arecont Vision is establishing processes and metrics to achieve faster support. Arecont Vision is strengthening its support team with new people, processes and systems. The company may have the same number of online and support calls as it did in 2012, but the business volume has tripled since then.
The team is better organized, and behaviors are being established to prepare for the installation of a help desk software solution to track service level agreements (SLAs), escalation procedures, etc. Technical support in the Glendale office opens at 5 a.m. Pacific time and closes at 6 p.m. Pacific, handling more than 91 percent of technical support calls (there is also technical support in Europe, and a French-speaking team in Montreal.) “We have come a long way in a short period of time,” says Sasha Ross, Senior Manager, Technical Support Department. “Our numbers are reflecting that. We are pleased with the progress we have made.”
Technical support calls reflect any product problems, and the nature of calls has changed as quality improvements have been put in place. In fact, many of the calls are now from integrators who are installing IP systems for the first time and need extra hand-holding. Arecont Vision technical support personnel go out of their way to avoid finger-pointing and to help customers diagnose a problem, even if the problem stems from another company’s product and is not related to the cameras.
"Overall, the process we use is
|
A robust quality control process
Arecont Vision is embracing best practices related to quality control. They have better testing facilities, are using new metrics, and have a new quality director. Quality meetings are held often. All products get full quality inspections -- two of them -- and there are no more issues with wrong labels or missing screws or other problems with the cameras. Overall quality metrics have improved, even as growth in the company’s volume has exploded in recent years. Return rates have plummeted; RMA (return merchandise authorization) rates have dropped three- or four-fold.
In addition to quality control, cameras are tested – how do they work in low light, bright light or mixed lighting? How does a camera work inside an enclosure? “Overall, the process we use is very robust,” says Darrel Tisdale, Arecont Vision’s Director of Quality.“Because we work with third-party software providers, part of our QA cycle is to look at how our cameras work with the top five [VMS] products [in the market].”